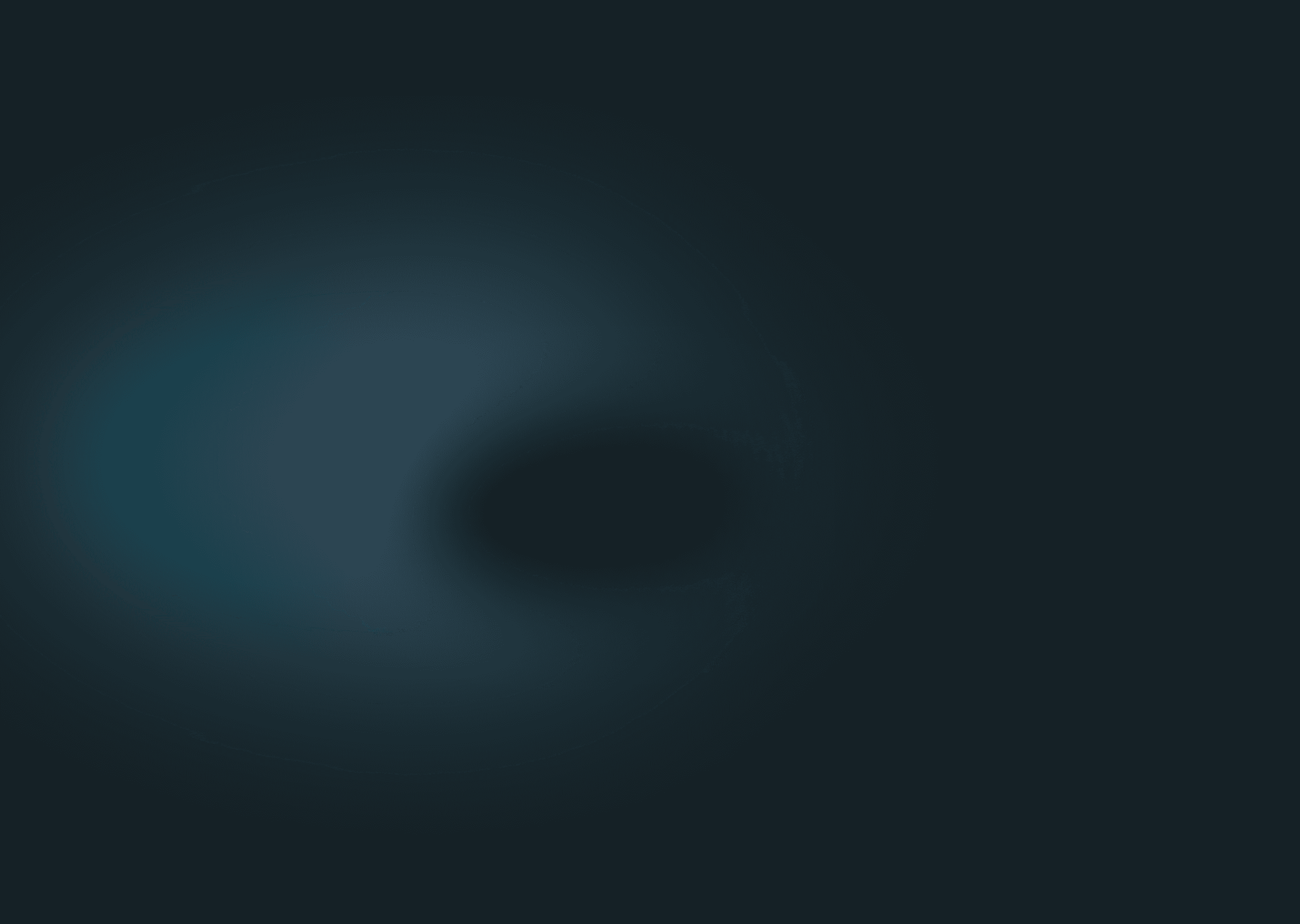
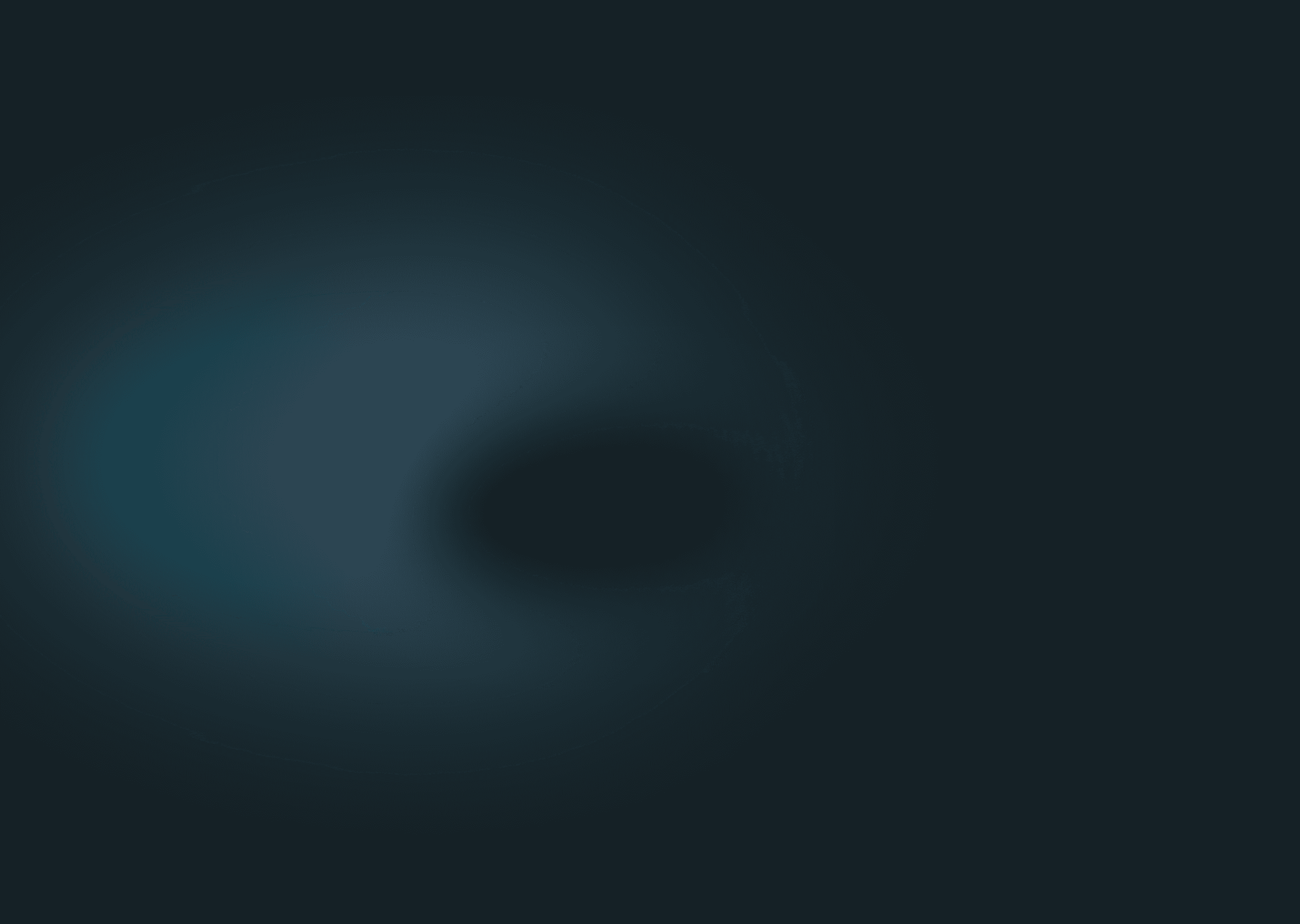
How Jermi Käsewerk Reduced Downtime and Optimized Efficiency with Things Twins
Get the Exclusive Case Study
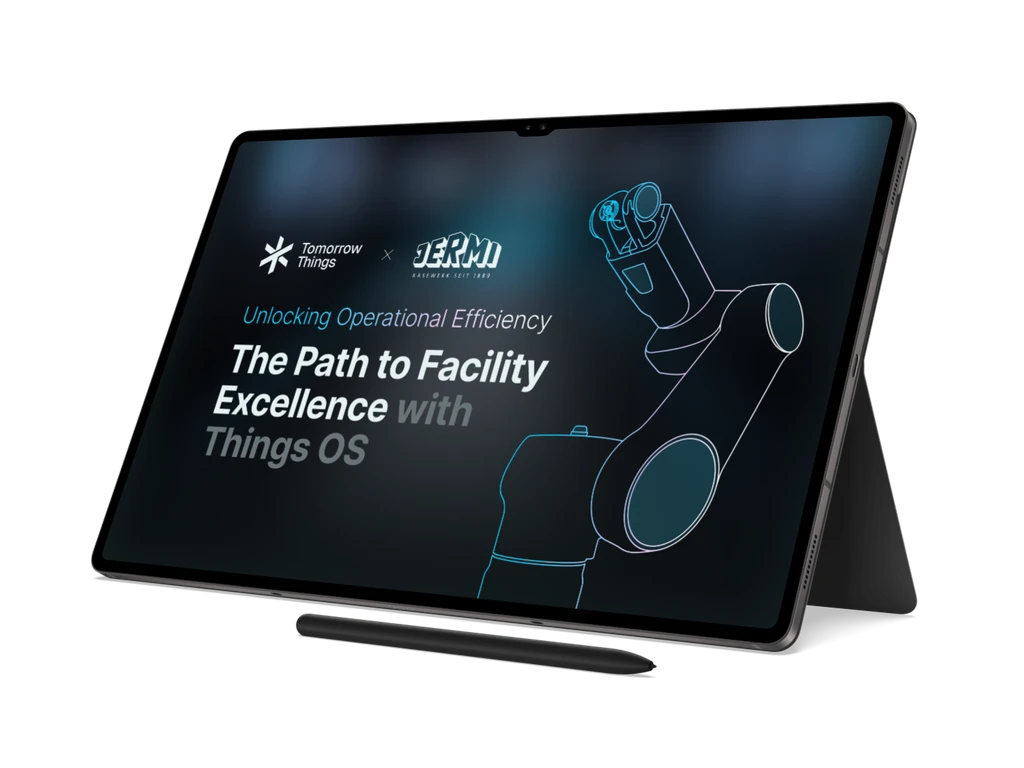
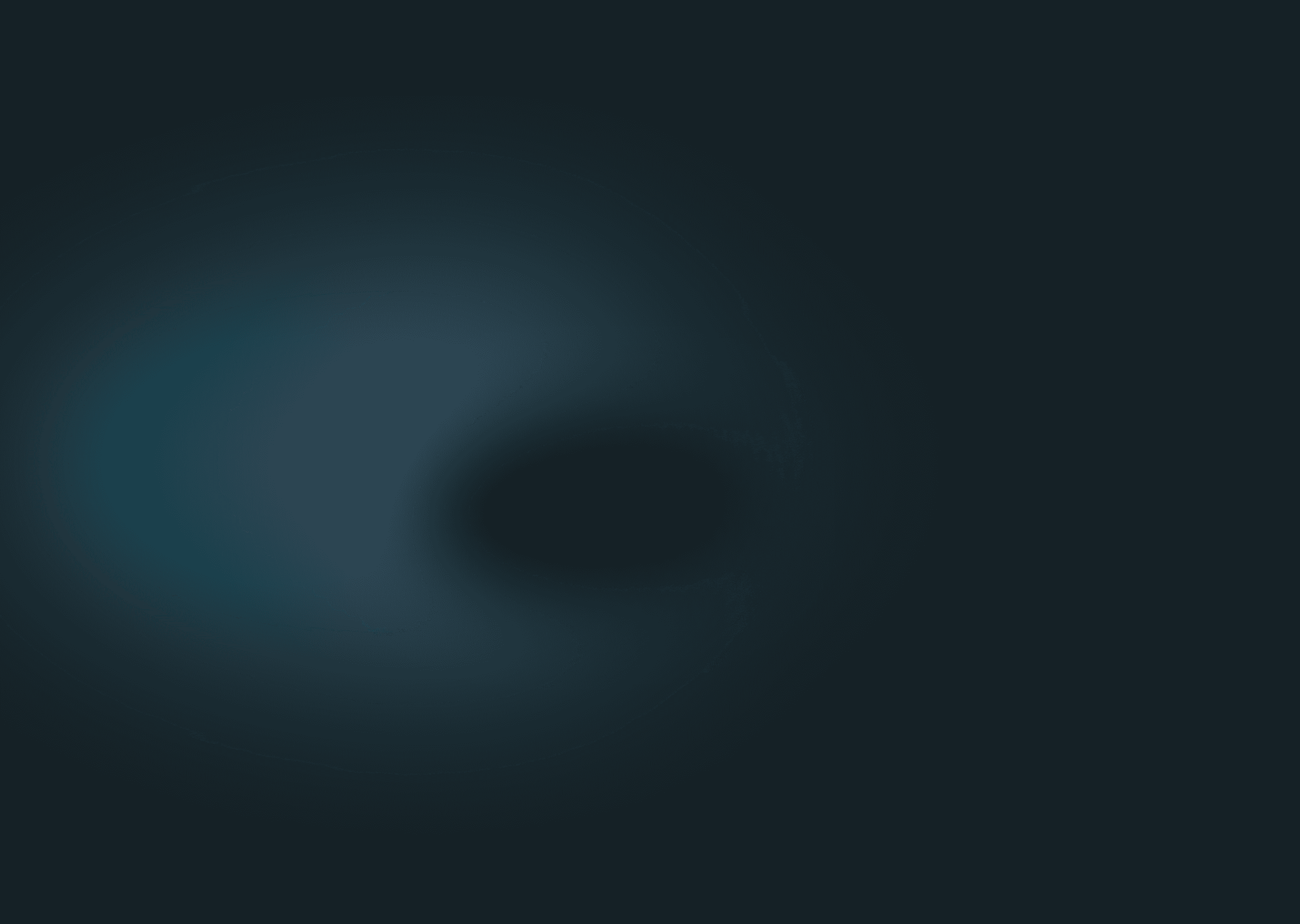
How Jermi Käsewerk Reduced Downtime and Optimized Efficiency with Things Twins
Get the Exclusive Case Study
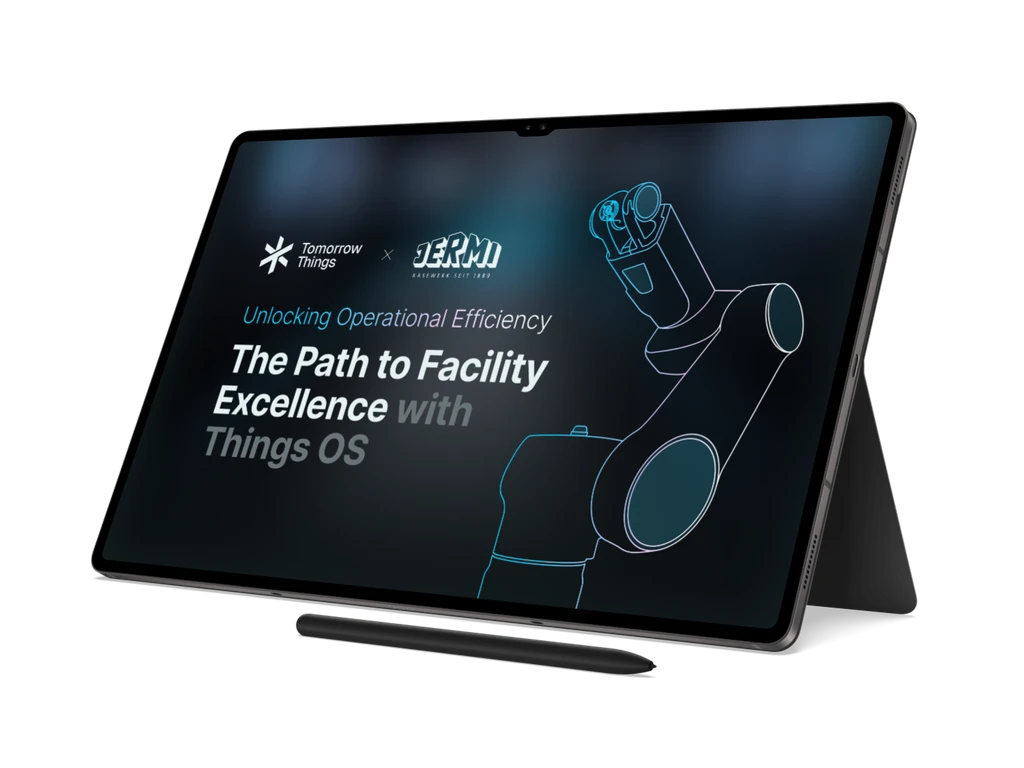
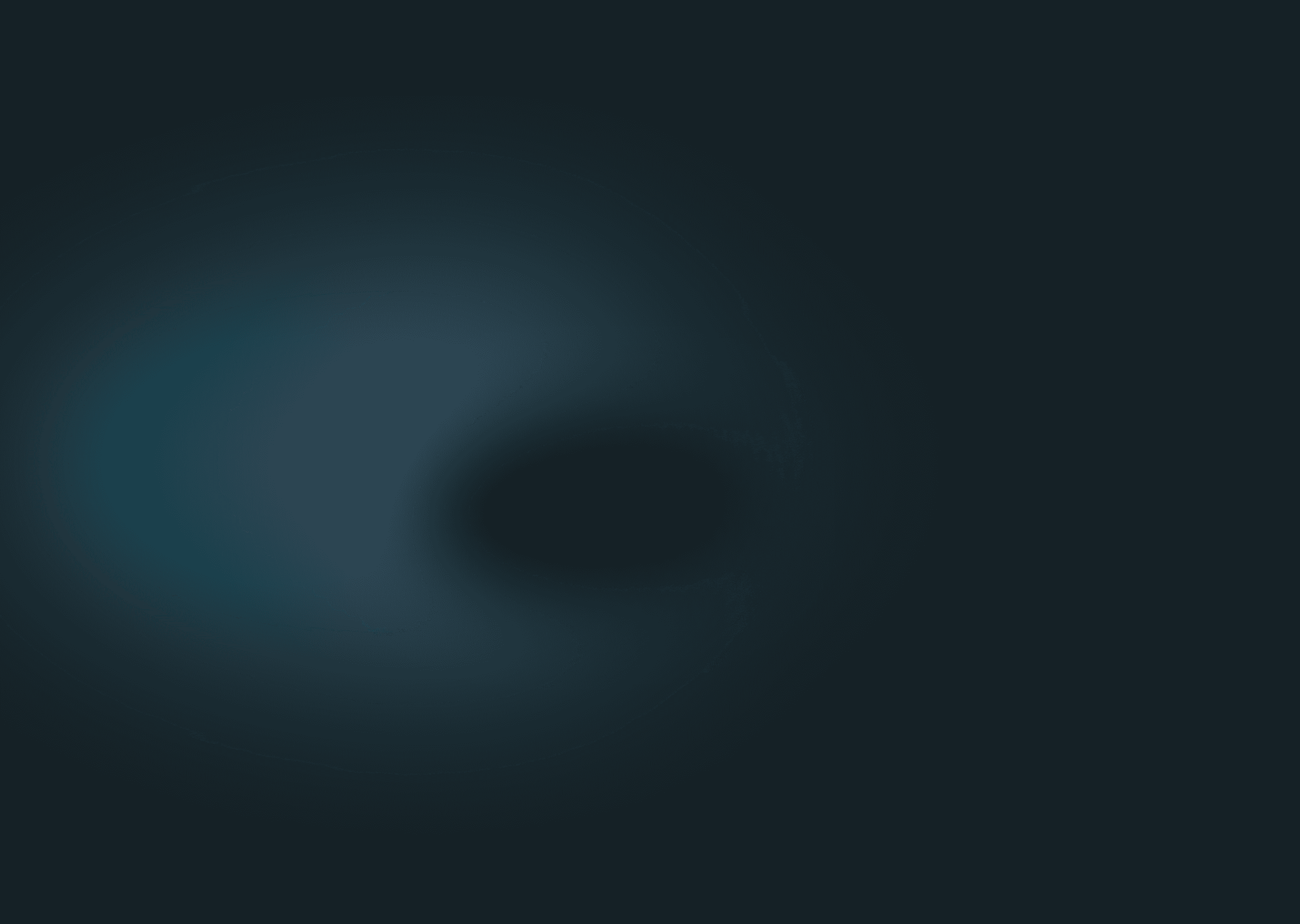
How Jermi Käsewerk Reduced Downtime and Optimized Efficiency with Things Twins
Get the Exclusive Case Study
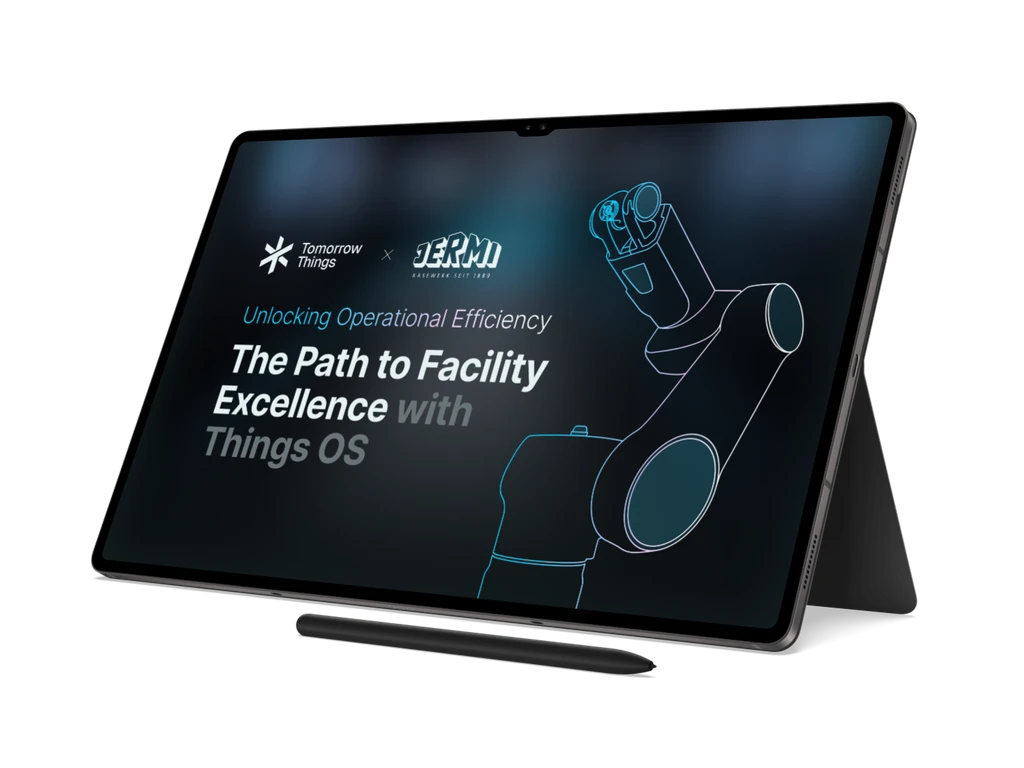
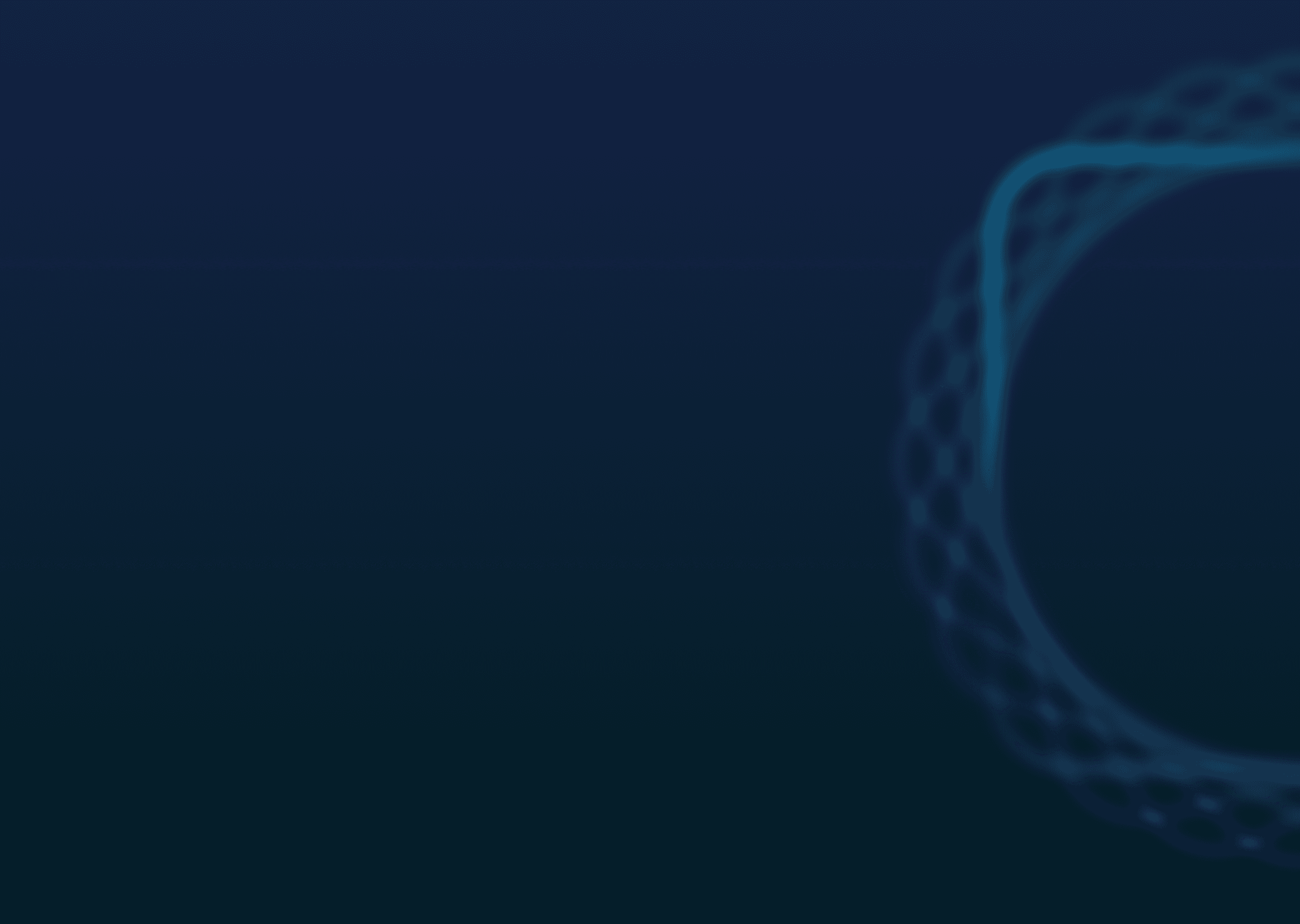
Discover How Jermi Käsewerk Transformed Its Manufacturing with Things OS
Jermi Käsewerk, a global leader in cheese manufacturing, set out to eliminate production blind spots, reduce costly downtime, and harness real-time data for smarter decision-making. With Things OS, they became the first in their industry to fully digitalize entire production lines—unlocking new levels of efficiency, cost savings, and competitive advantage.
What You’ll Learn in the Case Study:
Seamless Things Twin Implementation
With Things OS, Jermi integrated multiple machines, using pre-configured Blueprints to create a plug-and-produce Things Twin environment. Due to its success, they plan to almost quadruple the number of integrated machines.
Real-Time Data for Smarter Decisions
Operators and management were able to infer critical insights from automated, relevant data streams—enabling predictive maintenance and faster troubleshooting.
Minimizing Downtime & Maximizing Efficiency
Jermi Käsewerk improved Overall Equipment Effectiveness (OEE), reducing annual maintenance costs by €50,000 while streamlining production.
Ready to See the Impact for Yourself?
Fill out the form below to get instant access to the Jermi Käsewerk case study and learn how Things OS transformed their operations.
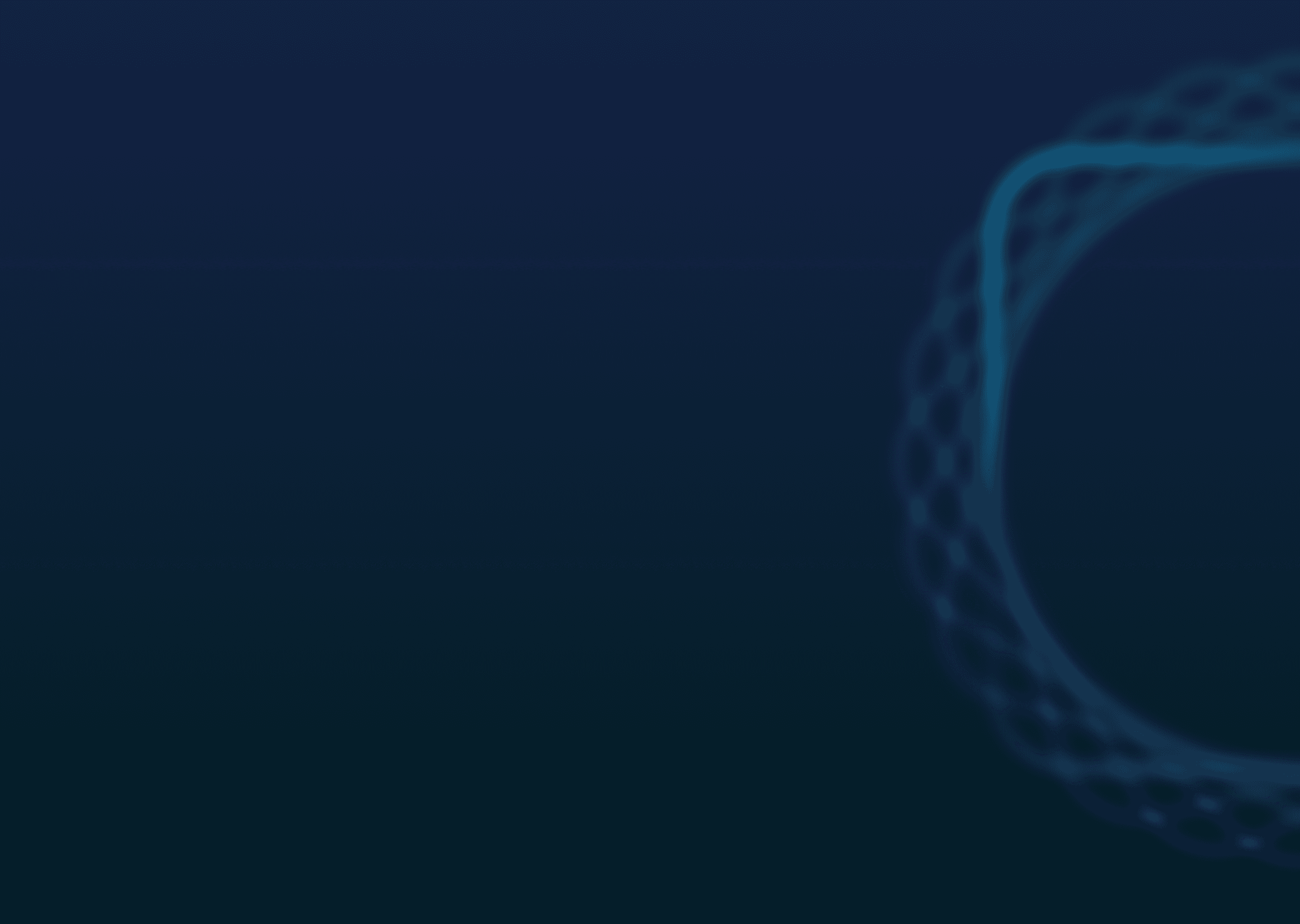
Discover How Jermi Käsewerk Transformed Its Manufacturing with Things OS
Jermi Käsewerk, a global leader in cheese manufacturing, set out to eliminate production blind spots, reduce costly downtime, and harness real-time data for smarter decision-making. With Things OS, they became the first in their industry to fully digitalize entire production lines—unlocking new levels of efficiency, cost savings, and competitive advantage.
What You’ll Learn in the Case Study:
Seamless Things Twin Implementation
With Things OS, Jermi integrated multiple machines, using pre-configured Blueprints to create a plug-and-produce Things Twin environment. Due to its success, they plan to almost quadruple the number of integrated machines.
Real-Time Data for Smarter Decisions
Operators and management were able to infer critical insights from automated, relevant data streams—enabling predictive maintenance and faster troubleshooting.
Minimizing Downtime & Maximizing Efficiency
Jermi Käsewerk improved Overall Equipment Effectiveness (OEE), reducing annual maintenance costs by €50,000 while streamlining production.
Ready to See the Impact for Yourself?
Fill out the form below to get instant access to the Jermi Käsewerk case study and learn how Things OS transformed their operations.
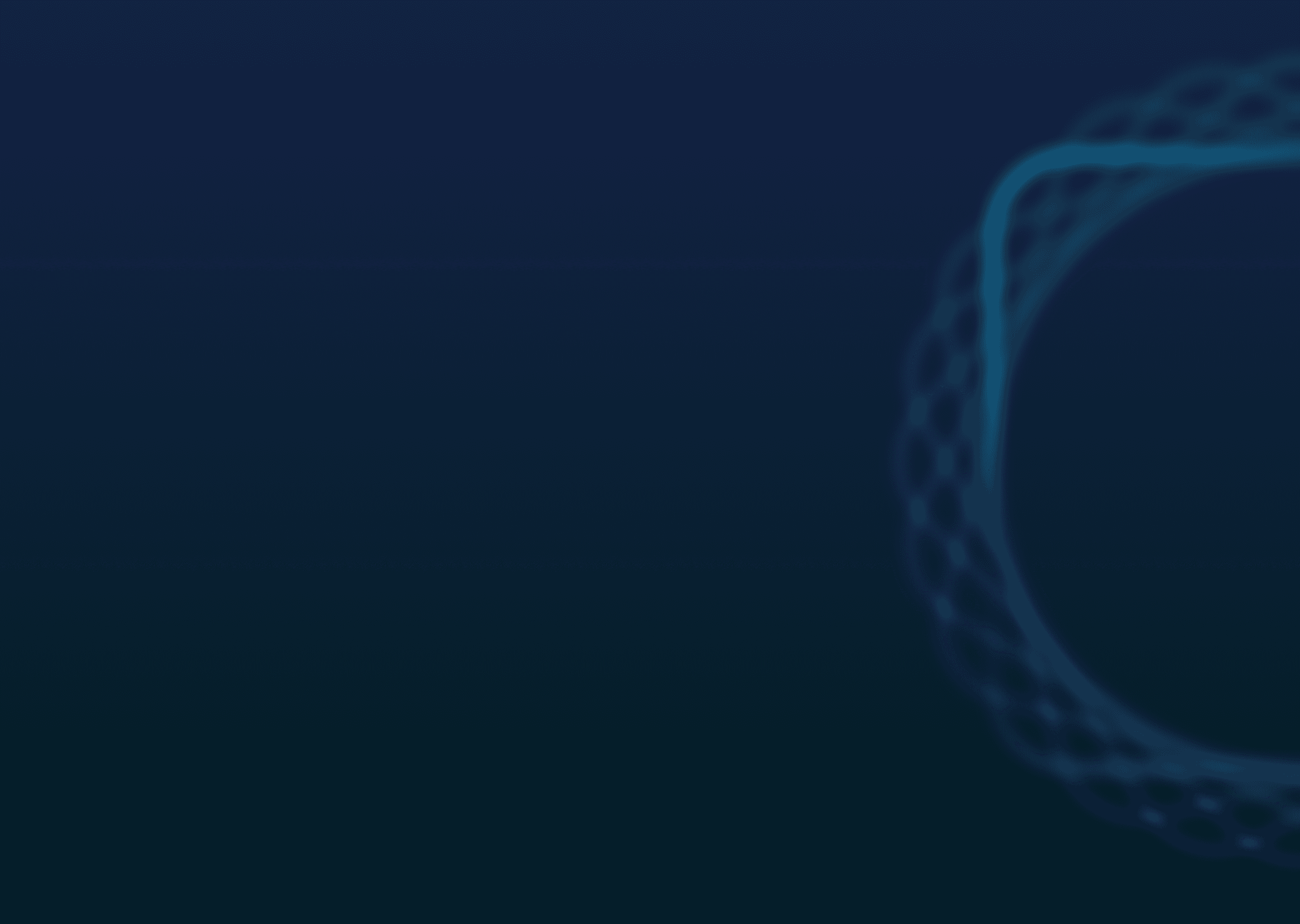
Discover How Jermi Käsewerk Transformed Its Manufacturing with Things OS
Jermi Käsewerk, a global leader in cheese manufacturing, set out to eliminate production blind spots, reduce costly downtime, and harness real-time data for smarter decision-making. With Things OS, they became the first in their industry to fully digitalize entire production lines—unlocking new levels of efficiency, cost savings, and competitive advantage.
What You’ll Learn in the Case Study:
Seamless Things Twin Implementation
With Things OS, Jermi integrated multiple machines, using pre-configured Blueprints to create a plug-and-produce Things Twin environment. Due to its success, they plan to almost quadruple the number of integrated machines.
Real-Time Data for Smarter Decisions
Operators and management were able to infer critical insights from automated, relevant data streams—enabling predictive maintenance and faster troubleshooting.
Minimizing Downtime & Maximizing Efficiency
Jermi Käsewerk improved Overall Equipment Effectiveness (OEE), reducing annual maintenance costs by €50,000 while streamlining production.
Ready to See the Impact for Yourself?
Fill out the form below to get instant access to the Jermi Käsewerk case study and learn how Things OS transformed their operations.
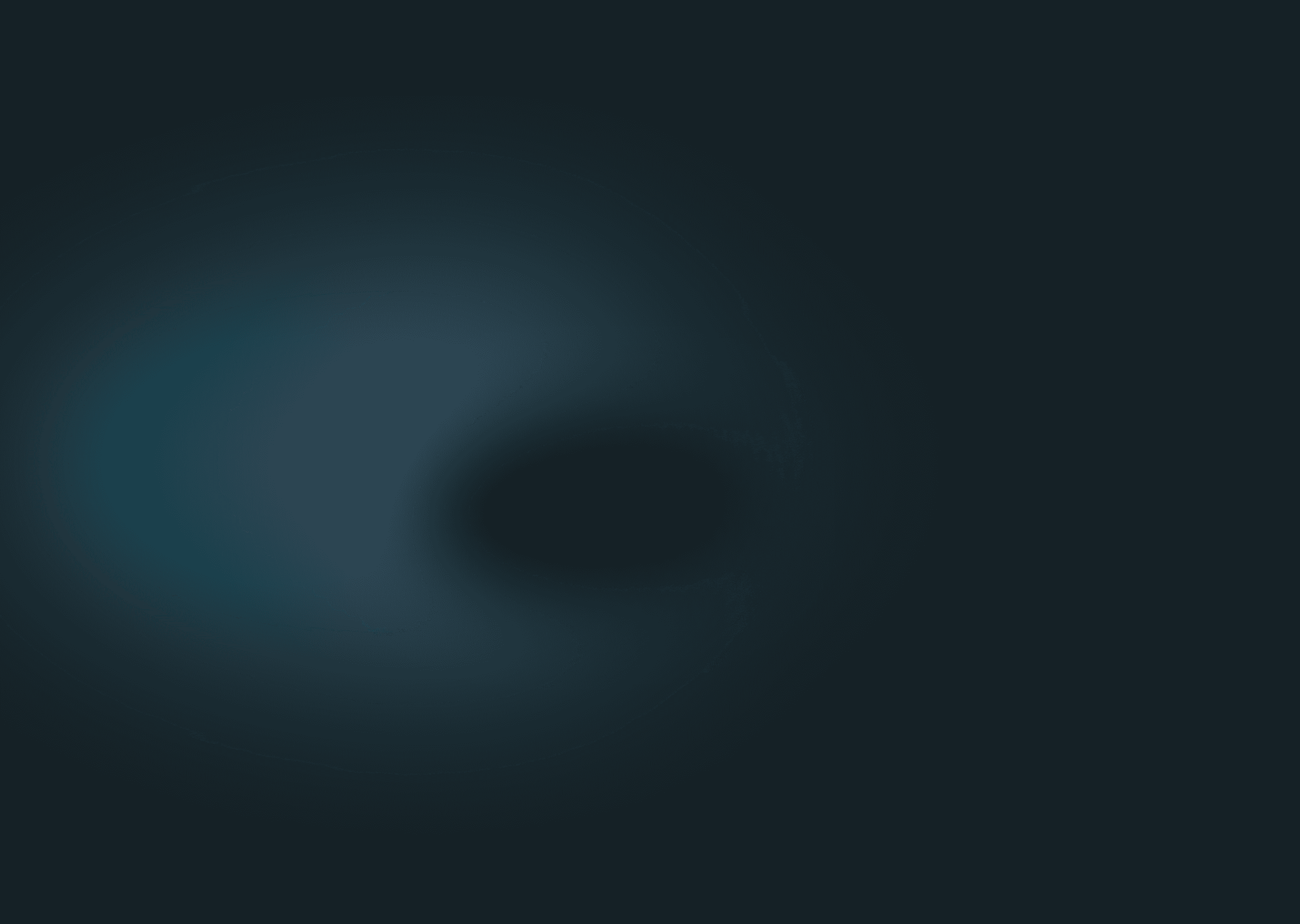
Why Read This Case Study?
Boost Efficiency & Cut Costs
Learn how Jermi Käsewerk optimized its production lines and reduced operational expenses.
Leverage a Plug-and-Play Digital Twin Solution
See how Things OS enables fast, vendor-independent machine integration with minimal effort.
Turn Data into a Competitive Advantage
See how manufacturers are leveraging real-time data not just to keep up—but to outperform the competition and redefine industry standards.
Enhance Machine Value for OEMs
Enhance your offering with built-in digital value, making your machines the obvious choice for operators.
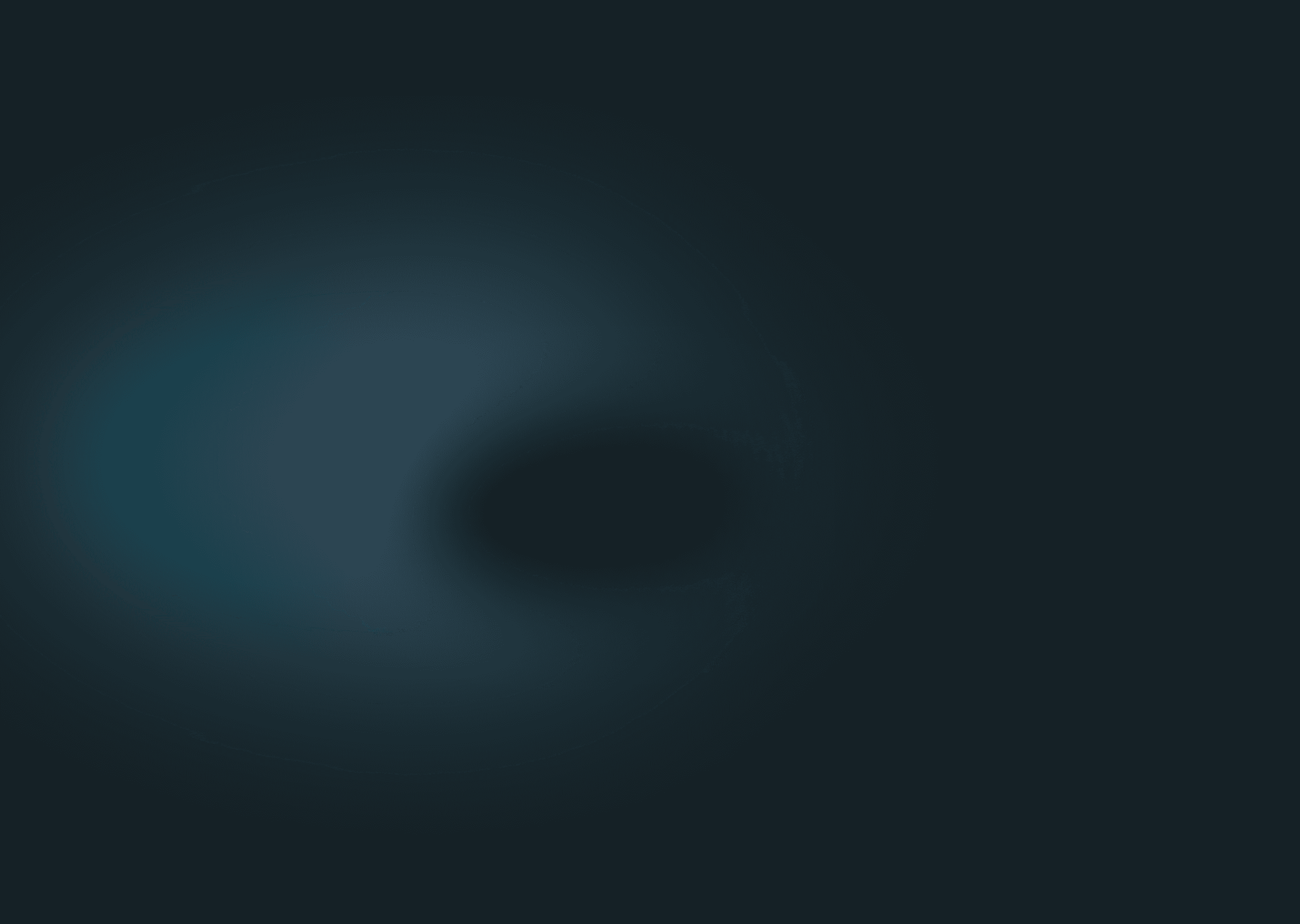
Why Read This Case Study?
Boost Efficiency & Cut Costs
Learn how Jermi Käsewerk optimized its production lines and reduced operational expenses.
Leverage a Plug-and-Play Digital Twin Solution
See how Things OS enables fast, vendor-independent machine integration with minimal effort.
Turn Data into a Competitive Advantage
See how manufacturers are leveraging real-time data not just to keep up—but to outperform the competition and redefine industry standards.
Enhance Machine Value for OEMs
Enhance your offering with built-in digital value, making your machines the obvious choice for operators.
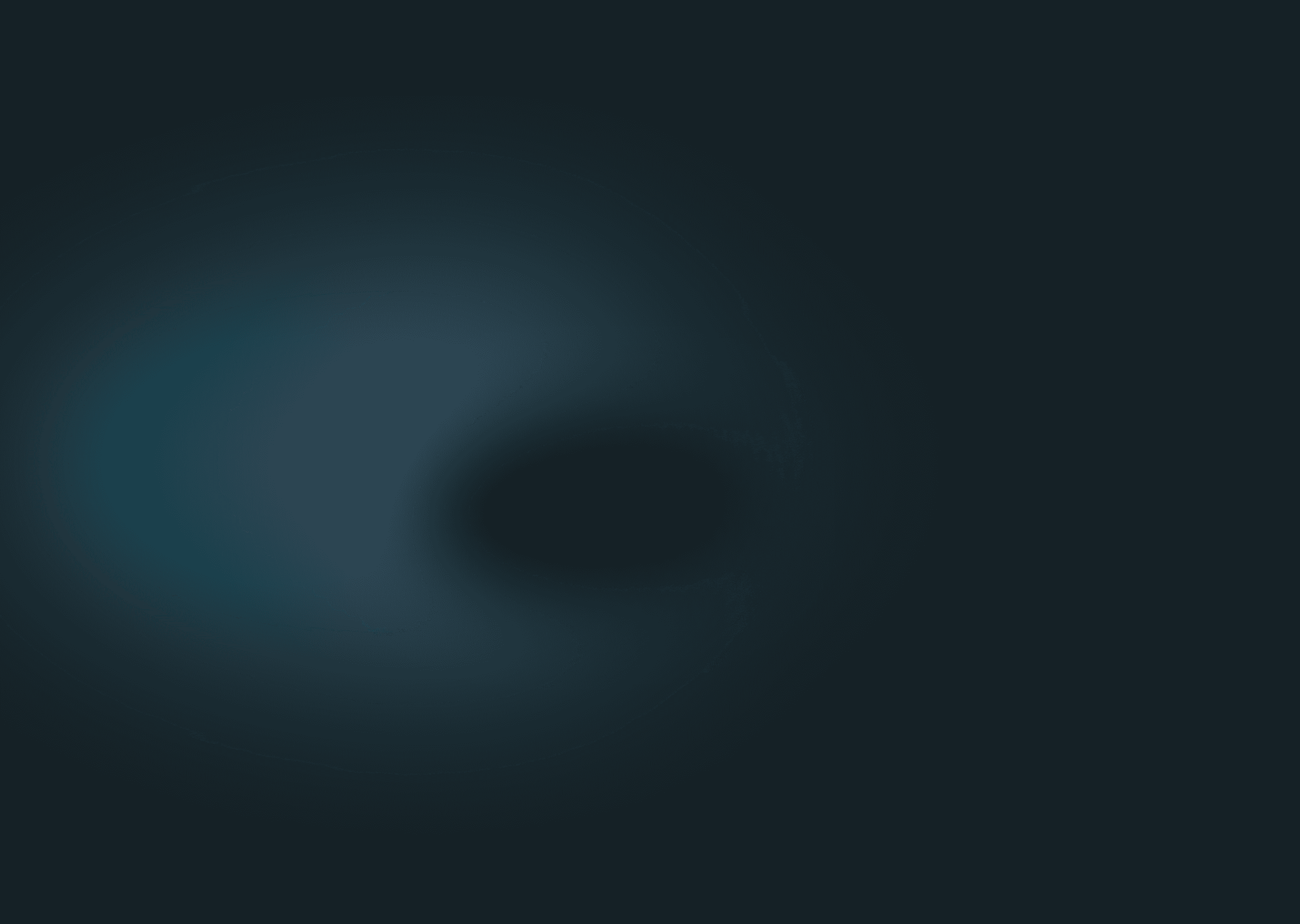
Why Read This Case Study?
Boost Efficiency & Cut Costs
Learn how Jermi Käsewerk optimized its production lines and reduced operational expenses.
Leverage a Plug-and-Play Digital Twin Solution
See how Things OS enables fast, vendor-independent machine integration with minimal effort.
Turn Data into a Competitive Advantage
See how manufacturers are leveraging real-time data not just to keep up—but to outperform the competition and redefine industry standards.
Enhance Machine Value for OEMs
Enhance your offering with built-in digital value, making your machines the obvious choice for operators.
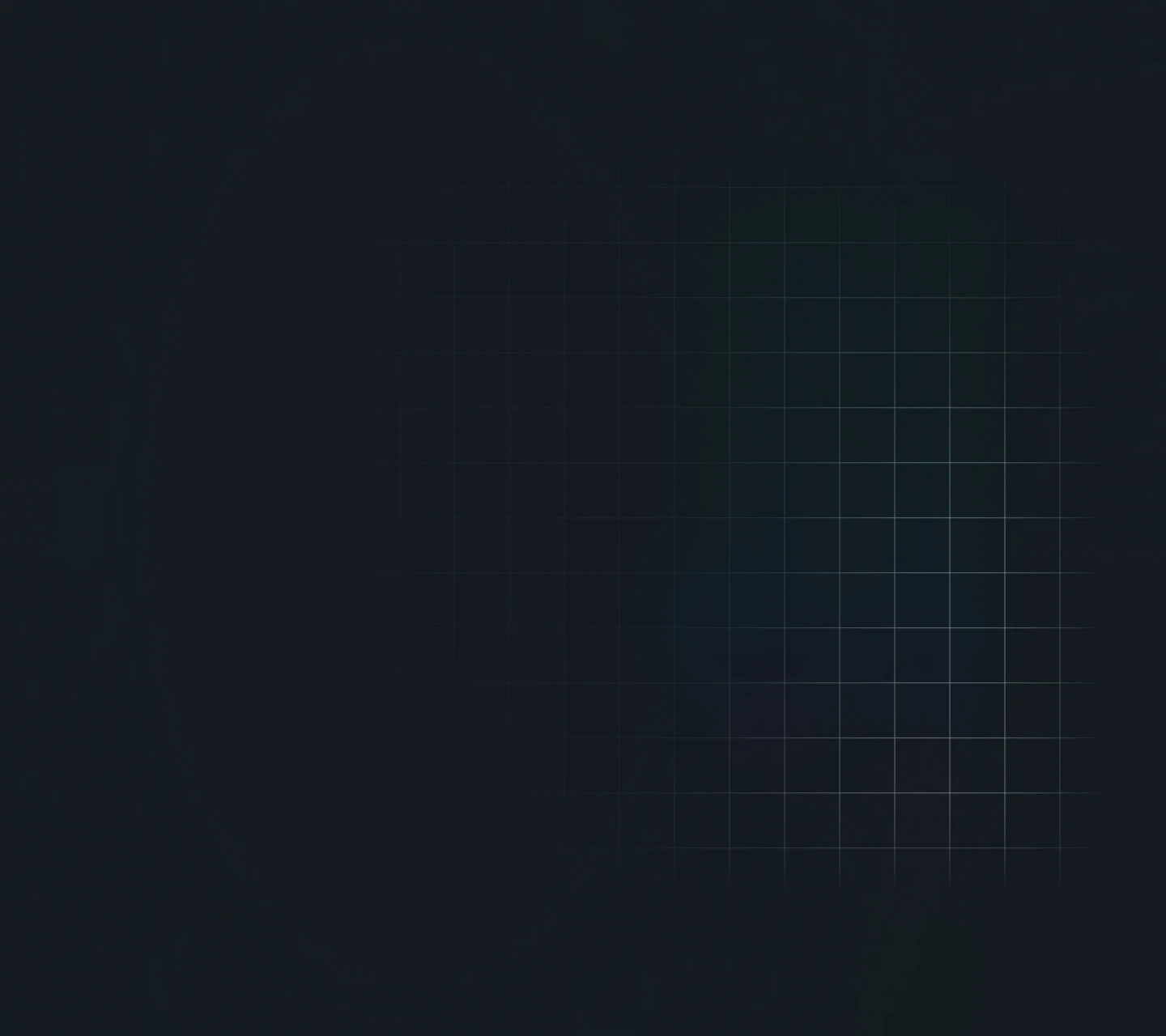
Gain a Competitive Edge Today
Download the case study and take the first step toward more efficient, data-driven manufacturing operations.
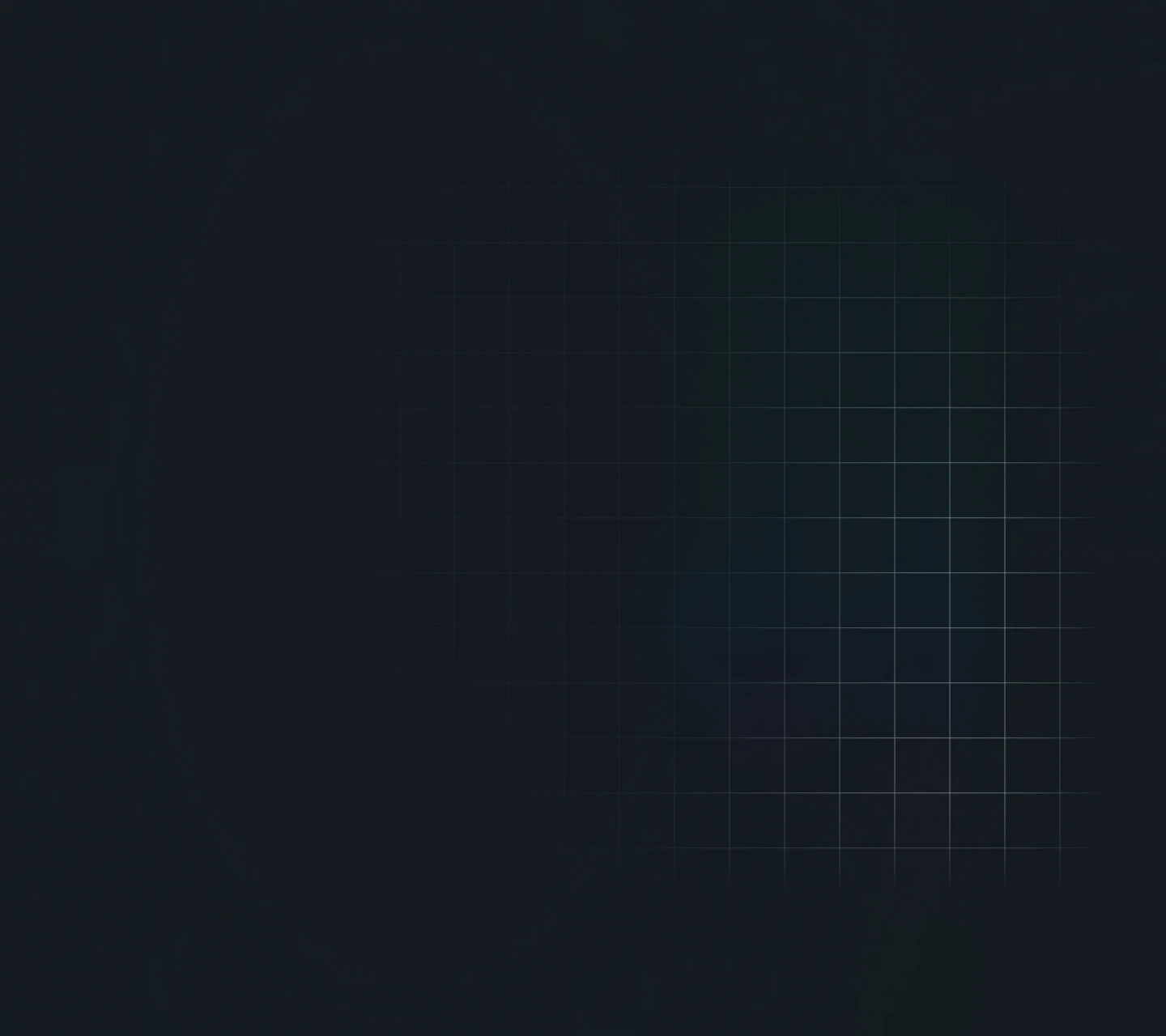
Gain a Competitive Edge Today
Download the case study and take the first step toward more efficient, data-driven manufacturing operations.
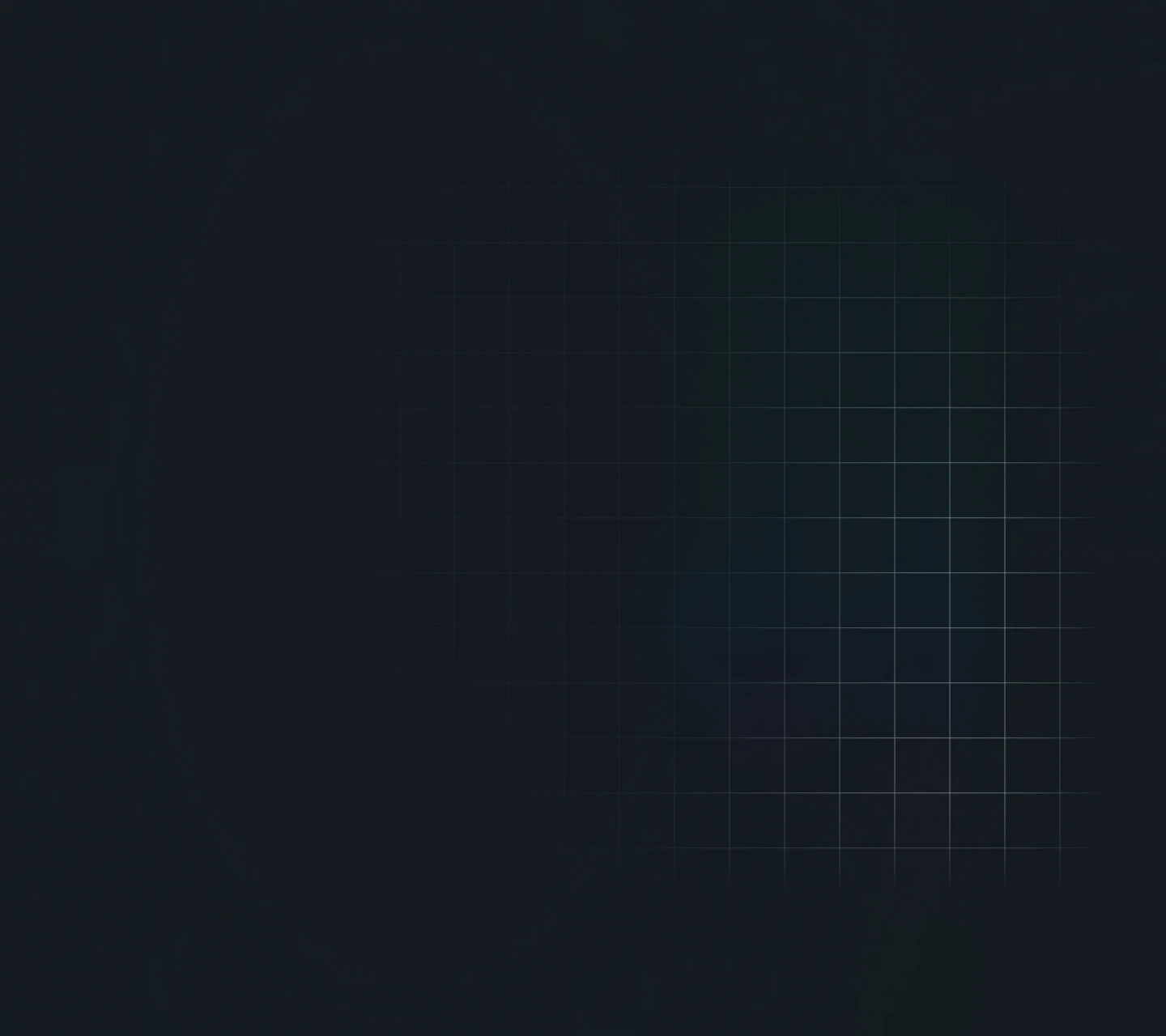