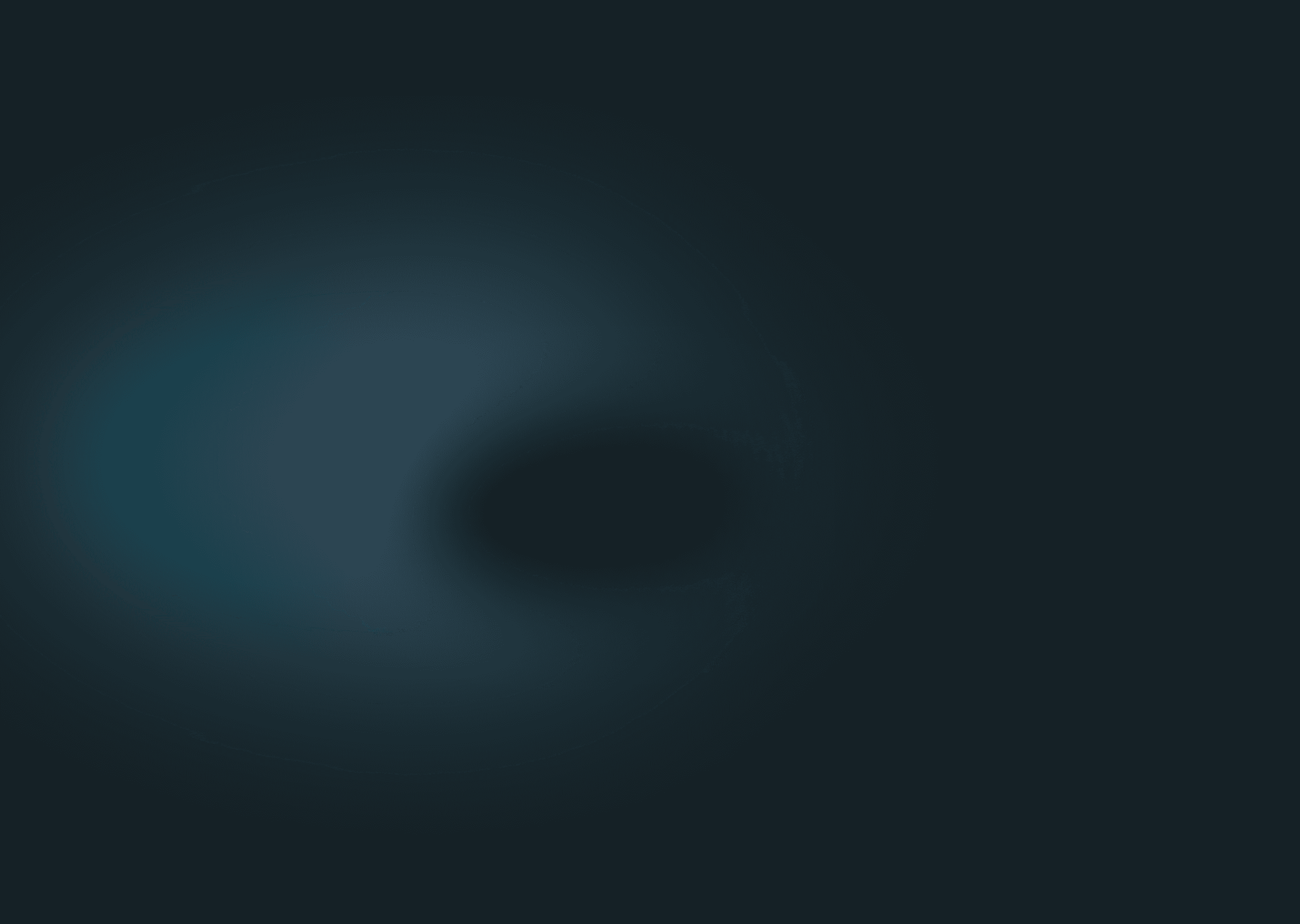
Save on manufacturing costs!
Get instant access to the Plastium case study – and see how Things OS is transforming manufacturing with real results and rapid ROI.
Discover how Plastium transformed its operations
Plastium, a leader in advanced plastics manufacturing, partnered with Tomorrow Things to unlock predictive insights from real-time machine data. With Things OS, they’ve paved the way for smarter, data-driven operations at scale.
Predictive maintenance that pays off
By avoiding over 50 hours of downtime per machine each year, Plastium achieves significant cost savings. Operations run more smoothly, and emergency maintenance is reduced.
Data-driven quality improvements
Thanks to better insights into production parameters, Plastium was able to reduce scrap and improve manufacturing quality.
15 minutes: Plug-and-play condition monitoring
Using Things OS, Plastium implemented real-time monitoring in just 15 minutes - enabling immediate access to machine health data and alerts, even during unattended shifts.